Warehouse management solutions: Ubiquicom for more efficient processes
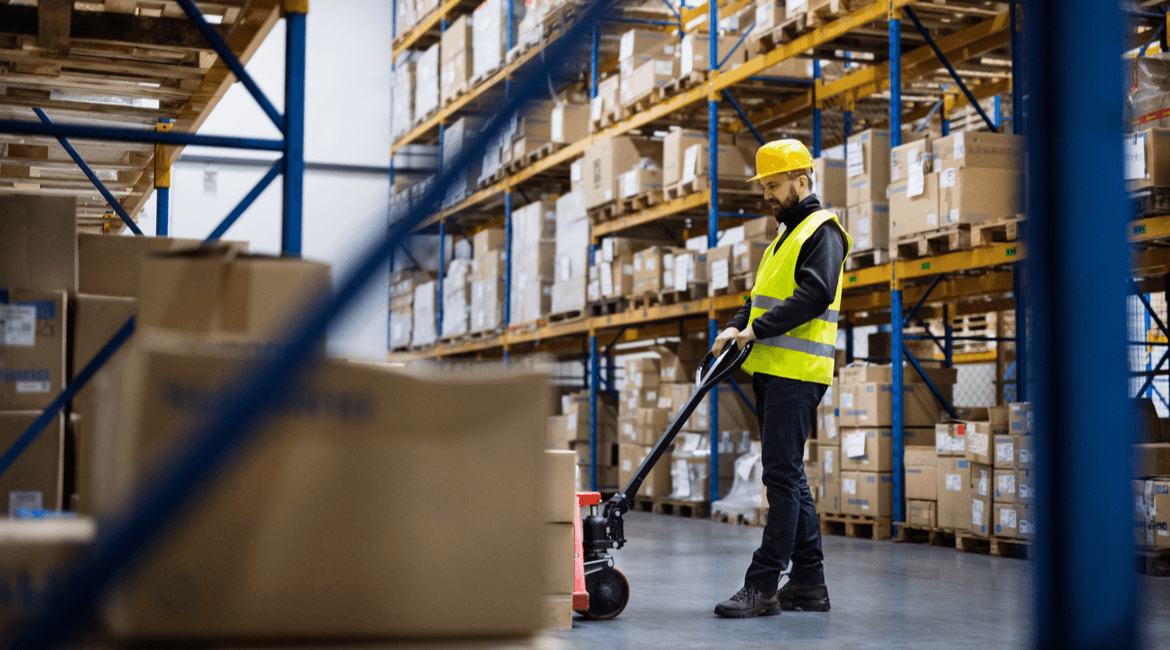
The optimization of material handling processes within warehouses is a priority for logistics companies. The rise of prices of raw materials, interruptions in supply chains, and an increasingly strong demand require the reduction of time and cost of operations.
These challenges lead companies to look at automation technologies with an increasing interest, thus driving the growth of a market that, according to forecasts, will reach a value of $ 30 billion by 2026.
With more and more companies focusing on these technologies, choosing the right partner becomes a strategic factor to stand out from the competition. Companies need scalable, flexible, and customizable solutions that can adapt to the needs of a complex and changing context such as the one at warehouses. That’s what Ubiquicom can offer, thanks to an approach based on continuous innovation and customization of its solutions.
Many applications with a single platform: Locator, the heart of the Ubiquicom offer
Non-standardized processes can lead to inefficiencies in the company’s asset management, including goods and material handling equipment.
Even today, this part is often entrusted to manual control done by workers, making the process long and often inaccurate. A greater visibility on the location of assets can address this issue, optimizing time and use of the vehicles more efficiently.
Ubiquicom’s offer is directed to this goal and revolves around the platform Locator for real-time location, tracking systems of people, vehicles, and assets, telemetry, and real-time management of complex location-focused events.
Based on standard protocols and architectures, Locator is a localization platform independent from the employed technologies and devices. Thanks to this, Ubiquicom has built on the solution a wide range of integrated applications that address distinct areas and needs.
SYNCHRO, revolutionizing material handling operations within warehouses using Artificial Intelligence
An example of these applications is SYNCHRO, the most innovative logistics and warehouse processes efficiency system on the market. The platform is based on standard architectures and protocols and can easily integrate with most of the existing Warehouse Management Systems (WMS).
SYNCHRO integrates various technologies – such as Artificial Intelligence and the Locator software – to support operations within the warehouse.
The localization software integration allows SYNCHRO to know, in real time and with extreme accuracy, the position of indoor and outdoor material handling equipment.
This allows companies to monitor the progress of operations, detecting possible delays and misalignments in the schedule. Thanks to integrated AI tools, SYNCHRO also makes it possible to reschedule tasks based on what is happening inside the warehouse at a given time. The sequence is thus optimized according to the available resources, reducing empty runs and, consequently, the cost and time of material handling operations.
Direct and indirect localization of goods, which one to choose?
To make warehouse processes efficient, it is not enough to know the position of the material handling equipment. Additional advantages, both for warehouse and production processes, can in fact be enabled thanks to the location of goods. Ubiquicom’s offer is able to support companies in achieving a greater view on internal processes, regardless of needs and applications.
The company’s portfolio includes both direct and indirect localization solutions.
The indirect localization is preferable in those contexts characterized by large volumes of objects to be located or for companies dealing with goods with a low value per unit. On the other hand, the direct localization is the best choice when the asset has a high added value, as in the case of luxury goods. In addition, this application supports the operation of companies where the production process is complex and the asset moves in different stations within a closed circuit.
Warehouse management: Ubiquicom solutions for indirect asset localization
The indirect localization provides the position of the goods starting from the direct tracking of the material handling equipment. The system uses several technologies: UWB infrastructure, onboard devices and height sensors on the forks for a very accurate tracking.
Depending on the need, it is possible to equip the forks with an RFDI reader, or equip the forklift driver with a barcode or QR reader.
The asset itself is traced through the use of passive (and therefore low-cost) technology, such as Barcode, QR code or advanced RFID, allowing the driver to identify the transported object without having to get off the vehicle, in order to speed up operations.
Data relating to the route stored by the Locator platform makes it possible to reconstruct movements and identify the point in the warehouse where the product was unloaded.
Direct localization of goods to optimize production and deliveries
The direct localization, as anticipated, is preferable in those contexts where the asset moves in a closed circuit. These are, therefore, goods with a complex production process and articulated in different stations within the same facility or in different locations.
In this case, knowing the exact location of the semi-finished or finished product can optimize production and allow a better delivery plan to customers. In these applications, the challenge for a technology provider is to balance the need for detection accuracy with cost reduction.
This is a need that Ubiquicom always keeps in mind when developing the offer for its customers. The range of solutions proposed by the company includes localization devices that exploit various technologies, such as Bluetooth Low Energy (BLE), which can extend battery life. In this way, energy consumption is reduced and the company’s investment can be amortized over time.
RTLS for the safety of material handling processes: PROXIMITY, Ubiquicom’s anti-collision system
Another key point of Ubiquicom is the continuous innovation of the products and systems offered to balance the different needs that arise within warehouses. The need to reduce the time of the processes often clashes with the need to increase the safety of workers and assets.
The solution capable of responding to these needs is PROXIMITY, the anti-collision system that uses UWB technology to ensure maximum levels of safety in warehouses and production areas.
Thanks to tags supplied to employees and devices mounted onboard the vehicles, PROXIMITY calculates in real time the distance between vehicle and worker or between two vehicles. If this distance is reduced beyond the set thresholds, the system activates automatic responses, including speed reduction or stopping of the vehicle.
Thanks to Ubiquicom’s commitment to innovating its offer, companies can get these benefits even without integrating the devices with the software.