Supply chain visibility: 4 technologies to integrate in your project
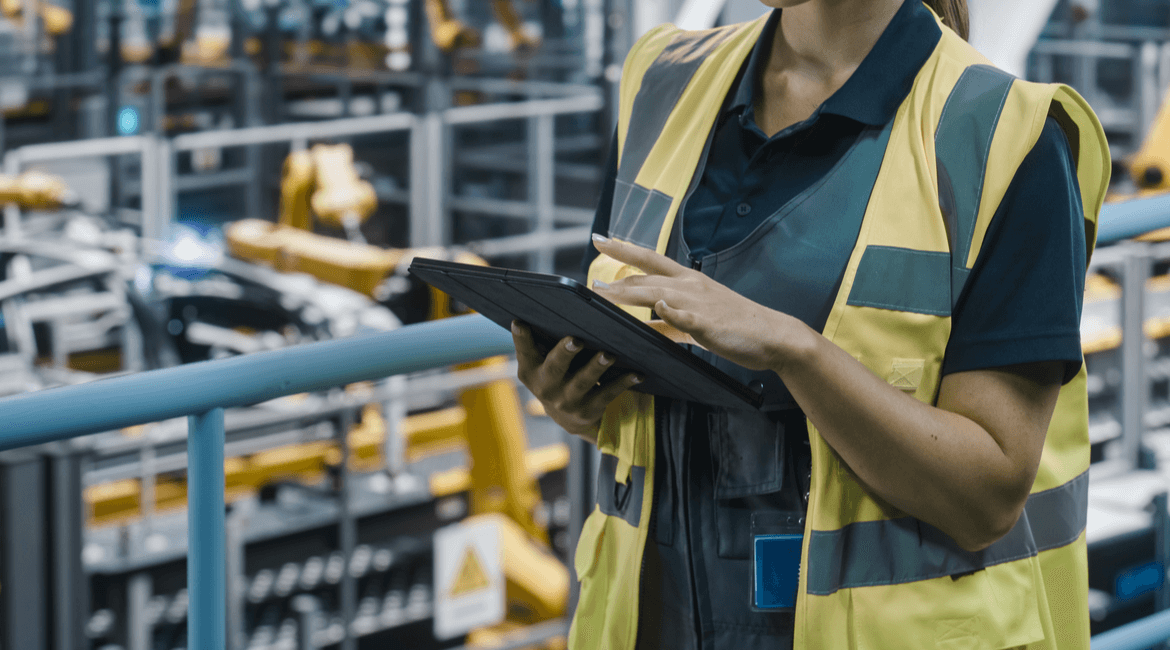
Supply chain visibility, meaning the visibility of processes within the supply chain, has never been more topical or important like now. Forbes in fact inserts visibility among the three top trends meant for the 2022 supply chain.
In the last two years supply chains have been put to the test, first by the pandemic and now by the conflict between Russia and Ukraine. Events that highlighted the frailty of global supply chains and challenged the resilience of companies.
The rise in prices of raw materials and energy is in fact halting what could have been the year of recovery for many companies. Difficulties that are added to those already posed by the digital and ecological transformation and that further push the demand for automation in the industry.
Automation that is essential to make processes more efficient, reduce human errors, waste and therefore also production costs.
1. IoT at the service of supply chain visibility
Among the other trends identified by Forbes for 2022 there are sustainability and resilience. Among them, the visibility of the entire supply chain takes on the role of enabler compared to the other two. This is because it’s not possible to make something more sustainable or resilient without an overall knowledge.
And to have greater understanding it’s necessary to measure. That’s how IoT becomes an enabling technology for visibility (and consequently resilience and sustainability) of the supply chain.
In logistics, visibility requires real-time, all-around monitoring of all resources involved in production and warehouse processes. Raw materials, semi-finished products, finished products, material handling equipment and workers: everything must work perfectly to respect production and delivery times.
Integration of data collected from IoT devices with other systems already in use within the company, such as the WMS, ERP and CRM, allows to enable numerous benefits.
2. Supply chain visibility, how to improve it thanks to RTLS systems
The introduction of RTLS can help in tracking the company’s resources, thanks to systems made of devices and software platforms. Devices mounted on the machine, or on tags supplied to the staff, able to track, in real time, the position of the worker or the vehicle. Depending on needs and context, it’s possible to use the Ultra wide band (for more accurate detection) or other technologies, such as GNSS and BLE. The software uses AI to analyze data, create custom reports in consideration of certain KPIs, and enable other benefits.
For example, the tracking of material handling equipment allows to speed up tasks. The worker is able to know in real time which vehicle is available and where it’s located. This reduces search time and human error to virtually zero.
The same applies to goods, which can be tracked indirectly starting from material handling operations conducted by tracked vehicles.
3. Artificial Intelligence
Artificial intelligence (AI) is another technology enabling supply chain visibility: it’s thanks to AI that data communicated by IoT devices are transformed into strategic insights.
In addition, starting from the use of these data, AI can create simulation models that help the company to better manage processes and spaces.
For example, it’s possible to create a mission report from the material handling equipment data. By analyzing the time employed, the load of each cart and the number of daily missions, AI can suggest strategies to improve the organization of tasks.
The same can happen in production processes. Here AI can take advantage of data collected by IoT sensors equipped on worker’s badges to monitor their productivity and suggest improvements.
In addition, thanks to IoT and AI, the company can also monitor accidents that have occurred (or nearly occurred) within production and storage areas. This allows to check critical areas for a increased security.
4. Digital Twin
The efficiency improvement strategies suggested by AI algorithms can be tested, at first, in a virtual reality. This is possible thanks to Digital Twin, virtual replicas of an asset (such as a vehicle) or a physical space (such as the warehouse).
The possibility to test efficiency improvement strategies in a virtual space allows to identify the most correct one. In fact, thanks to digital twins, the company can verify the impact that the suggested change could have on the resources involved in the processes.
In addition, costs and time for implementation are significantly reduced.