TrackVision
Telemetry and IoT for remote management and monitoring of industrial vehicles and equipment
Advanced fleet management software with Telemetry and IoT sensors
TRACKVISION is a cloud driven IoT software platform designed for industrial vehicles and equipment fleet management, supporting fleets ranging from 10 to 10,000 units. It is compatible with all vehicles’ brands and models.
With real-time telemetry data from the onboard Telematics Box, TRACKVISION provides a comprehensive view of fleet performances. Its intuitive interface allows remote monitoring and enables customized configurations tailored to specific vehicle types and operational needs.
How can you track industrial vehicles in real time? With TRACKVISION you get key insights to enhance fleet efficiency and full visibility on location, performance, and usage, including:
- Vehicle operating hours
- Collisions log
- Real-time location tracking
- Usage conditions
- Battery status
- Maintenance alerts
- Remote diagnostics
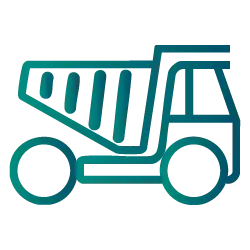
Articulated dumper
Crawler crane
Bulldozer
Mining excavator
Mining shovel
Mining truck
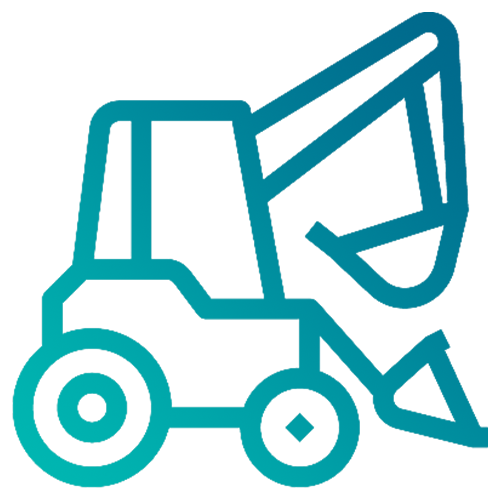
Excavator
Wheeled Loader
Compactor
Crane
Aerial Platform
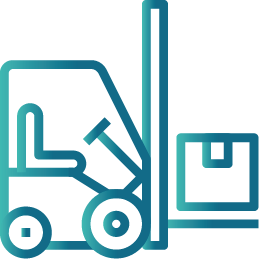
Forklift
Wheel loader (wheel loader or front loader)
Excavator
Bulldozer
Hoftrack
Tractor
Loader
Sports field & pitch mowers
Golf buggies
Commercial & Industrial Cleaning Machines
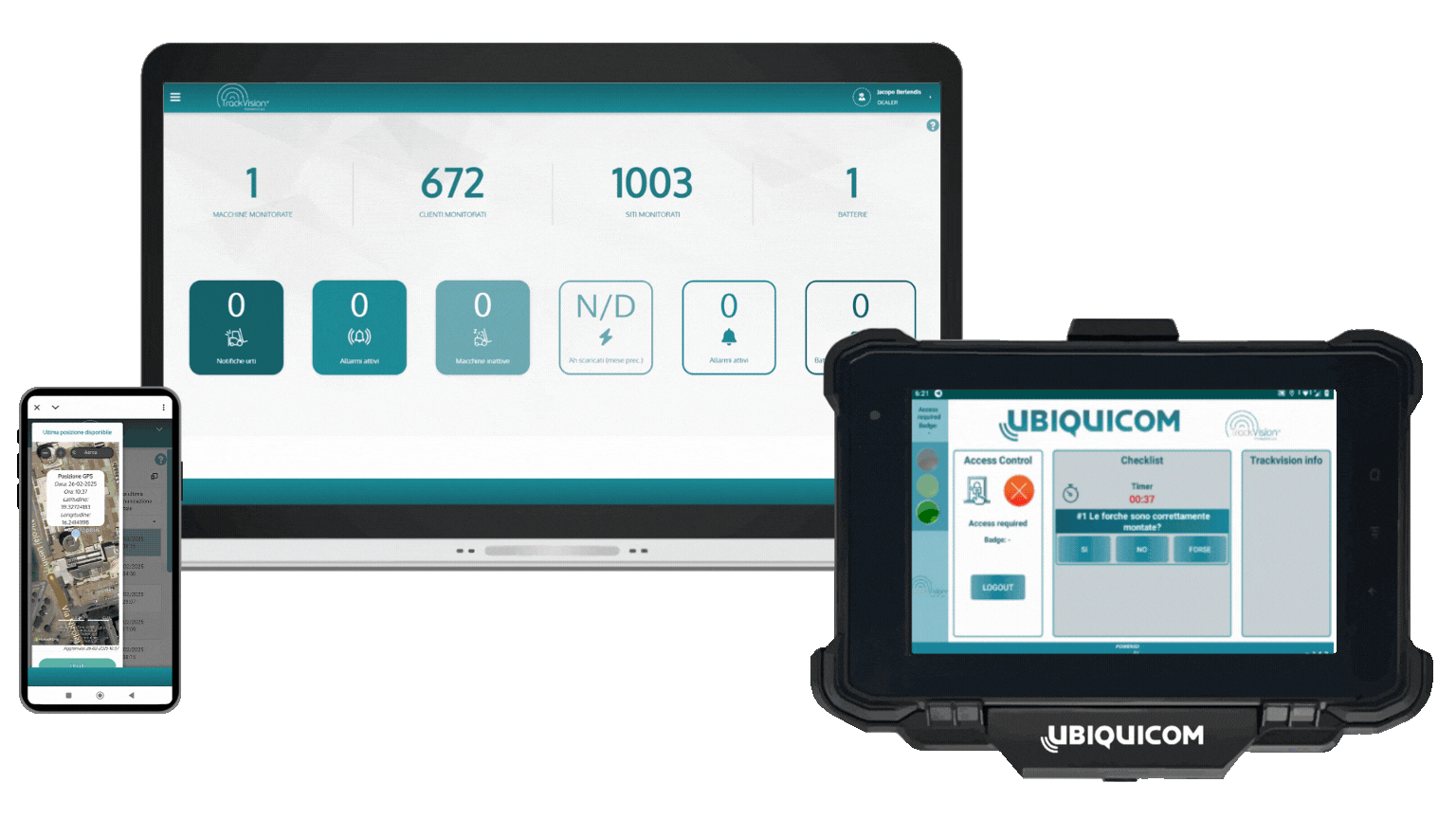
TRACKVISION empowers dealers to offer added value to sales or rentals through data-driven services.
Key Advantages:
- Tailored commercial solutions based on actual vehicle usage data
- Seamless service integration for remote diagnostics and advanced safety features
- Enhanced customer retention with proactive support
- Simplified mixed-fleet management across brands and vehicle types
Dealers can remotely track individual vehicles, monitor performance, and analyze key parameters such as real-time location, usage history, and maintenance needs.
With remote diagnostics, potential issues can be identified and resolved early, minimizing downtime, reducing repair costs, and optimizing spare parts inventory management.
For businesses investing in industrial vehicle fleets —whether through leasing or purchasing — TRACKVISION offers significant cost savings and operational efficiencies.
Key Benefits:
- Lower operating costs through smarter asset utilization
- Optimized maintenance schedules with reduced downtime
- Remote fault diagnostics for quicker issue resolution
- Improved safety through operator behavior monitoring
- Reduced environmental impact via resource-efficient operations
Real-time telemetry provides full visibility into fleet location, performance, and usage, enabling data-driven decision-making and optimized fleet sizing.
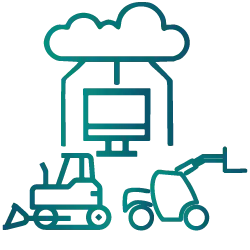
TRACKVISION, with a single platform, seamlessly manages fleets with diverse vehicle types, brands, and models.
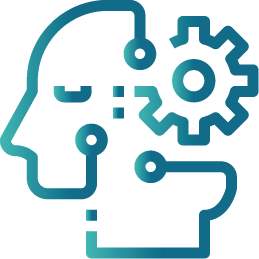
Using CAN-bus integration, TRACKVISION collects and processes real-time machine data, offering in-depth insights on fleet performance.
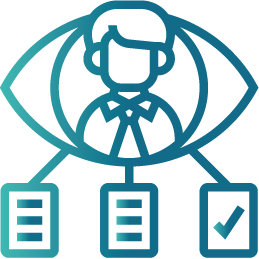
UBIQUICOM ensures that customers maximize their investment with dedicated after-sales support and comprehensive training programs.
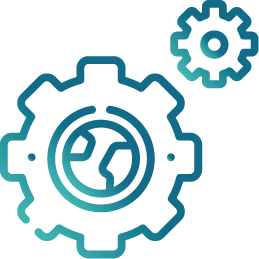
TRACKVISION integrates smoothly with ERP, MES, and WMS systems, ensuring streamlined workflows and data synchronization.
IoT—RTLS Connected Ecosystem: Integrated & Modular
UBIQUICOM offers a comprehensive suite of connected and intelligent solutions, ranging from remote telematics and diagnostics to advanced safety, location tracking, and process optimization tools for industrial and logistics environments.
INDUSTRIAL VEHICLES REMOTE DIAGNOSTICS & MAINTENANCE
TRACKVISION’s SHINDAN add-on enables advanced remote diagnostics, offering:
- Initial diagnosis of faults remotely, with drastic reduction of on-site trips
- Software issue remote management for faster resolutions
- Optimized spare parts inventory and management
- Enhanced customer service: quicker tech support, reduced downtime, improved fleet efficiency and safety
WORKPLACE SAFETY & COLLISION PREVENTION
TRACKVISION enhances workplace safety with key features, including:
- Pre-operational checklists via the onboard vehicle tablet
- Controlled operator access to vehicles
- Automatic speed limitation (in pedestrian zones, near vehicles, or post-collision)
- Usage restrictions outside designated work hours
- Real-time impact detection and analysis
- Near-miss incident logging
- Integration with PROXIMITY anti-collision systems
RTLS & ASSET TRACKING
LOCATOR is a real-time tracking platform for vehicles, assets, and personnel, enabling efficient process management and improved operational visibility.
PROCESS OPTIMIZATION WITH SYNCHRO
SYNCHRO leverages location data and AI to optimize resource orchestration in high-intensity warehouses, streamlining workflows and boosting efficiency.
How does the fleet management system work?
The Telematics Box integrates with the vehicle’s CAN Bus, enabling real-time telemetry data collection and precise location tracking.
The 4.0 Interface functions as an operator badge reader and controls vehicle activation and usage restrictions.
Onboard Vehicle Tablet Features:
- Operator badge reader for secure access to equipment
- Pre-operational checklists
- Anti-collision alerts and zoning features
- Sensor data collection (optional)
- Location-based applications (with LOCATOR)
- Mission management and workflow optimization (with SYNCHRO)
TRACKVISION is a fully cloud-based (SaaS) solution that integrates seamlessly with other enterprise applications via API.
Contact Us for a Demo
Advanced telemetry system for remote management of an entire fleet of vehicles
A suite of tools and services for data-driven fleet management of cleaning equipment