CLS
Remote management and iDAC telemetry system for a fleet of 5,500 forklifts with processes optimisation
An advanced telematics technology platform enables CLS to manage the entire fleet of forklift tracks from an Industry 4.0 point of view, for a true integration of the logistics and production processes.
CLS – CGT Logistica Sistemi, which forms part of the Tesya Group, has for 70 years been focussed on the sale, hire and support of forklift trucks, vehicles and equipment for every sector of goods handling and logistics. It has headquarters in Carugate (Milan), a workforce of more than 300 people, 11 branches, 9 operating centres, 180 mobile workshops, more than 5,500 vehicles on hire and 150 models of forklift trucks with a load capacity of up to 56 tonnes.
The requirements
The Customer required an advanced telemetry system which enabled state-of-the-art and universal integration of the entire fleet of vehicles (currently and in the future) that could be controlled remotely, which was able to adapt to all the needs of modern warehouses from an Industry 4.0 point of view in order to control and act on the operating flows of the logistics vehicles.
The system needed to be versatile and modular, able to adapt to new requirements with the addition of functionalities, providing a future-proof product which could keep in step with the emerging needs dictated by the digital transformation of the companies. It also had to be able to interface with existing HW/SW systems, both on the vehicle and in back-end mode.
The aim the customer wished to achieve was to offer value-added services to its clients to improve the industrial processes, streamline the procedures and optimize its business.
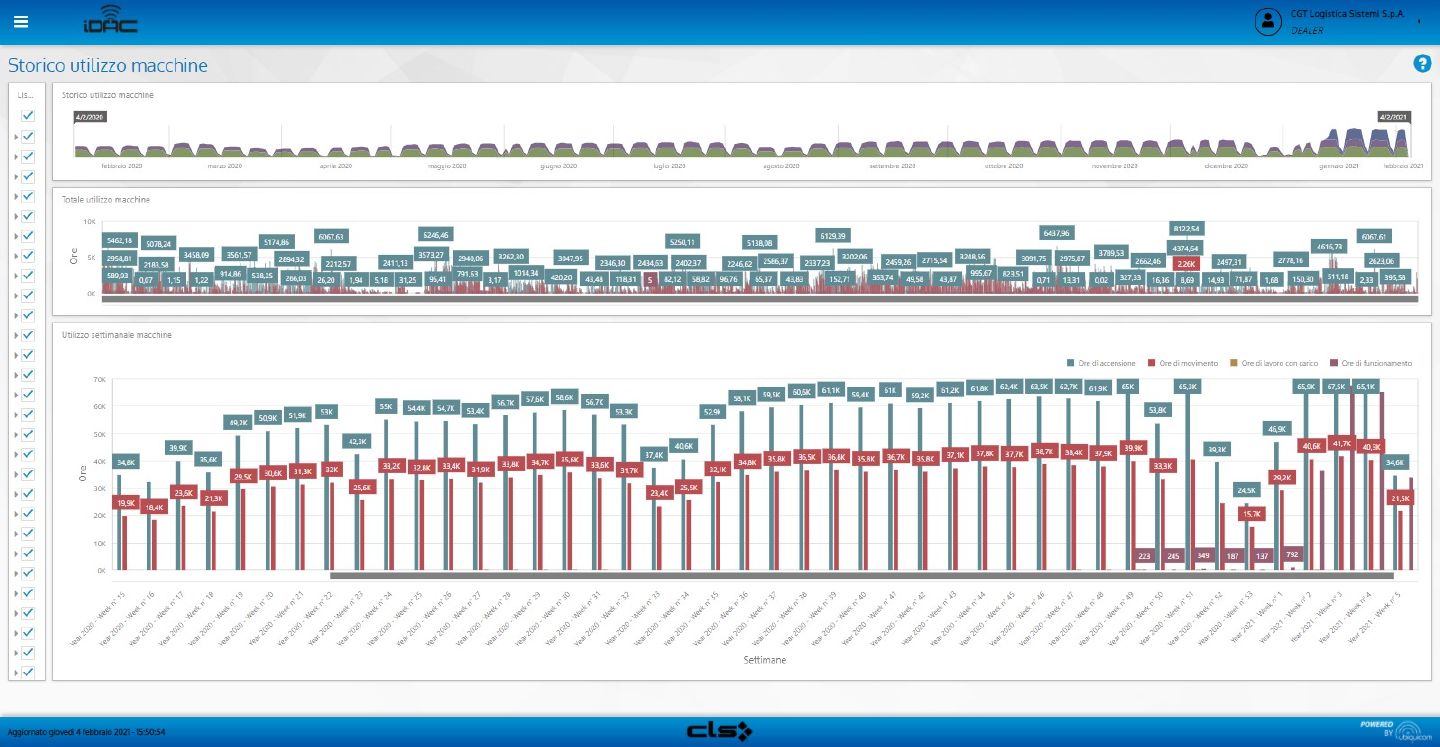
The solution developed by UBIQUICOM
Ubiquicom developed both the Hardware and Software components of the new advanced telemetry system iDAC.
The system consists of an online platform accessible with a normal Internet connection and integrated with the Customers SAP management system, a hardware component – the telemetry box – with in-built CPU, installed on the CLS which communicates with the cloud-based web platform through an IoT data card and through the WiFi modem, and an operator interface 4.0 which incorporates a badge reader so that the machine can only be started by authorised personnel.
Ubiquicom also developed a series of made-to-measure functions for CLS which have a dual purpose.
For the CLSdealer these functions allow a reduction of the OPEX, thanks to the possibility of carrying out remote diagnostics, predictive and preventive maintenance and monitoring of improper uses (battery consumption, collisions, …). From the dashboard it is possible to access strategic insights for operations and marketing, access use trends etc. Moreover, it is possible to also manage ad-hoc pricing models (pay-per-use / location-based).
For the final customer, iDAC enables services to be provided for preventing dangerous or prohibited uses, enabling use of the vehicle on the basis of the operators qualifications, monitoring times of use and signalling inactivity, and controlling checklists of operators.
Ubiquicom has set up a total of more than 2,500 installations and supported CLS for all aspects regarding consultancy, installation and training of personnel.
Results
Each CLS uses an advanced telematics technology platform which integrates the entire fleet of vehicles. The new system enables traditional machinery to be integrated digitally in the production processes: it sends and receives data and operating instructions which can be consulted and managed in real time through the portal and web interfaces.
By using iDAC, CLS can remotely measure the parameters of use of the machines, receive signals of faulty machines, identify the position of the machine indoors and/or outdoors, control accesses (and thereby only allow use of the machine by qualified and authorised personnel), prevent vehicle/man and vehicle/vehicle accidents (anti-collision) thanks to an automatic zonal slowing down system.
CONTACT US