Logistics management 4.0: how to make warehouse processes and resources more efficient
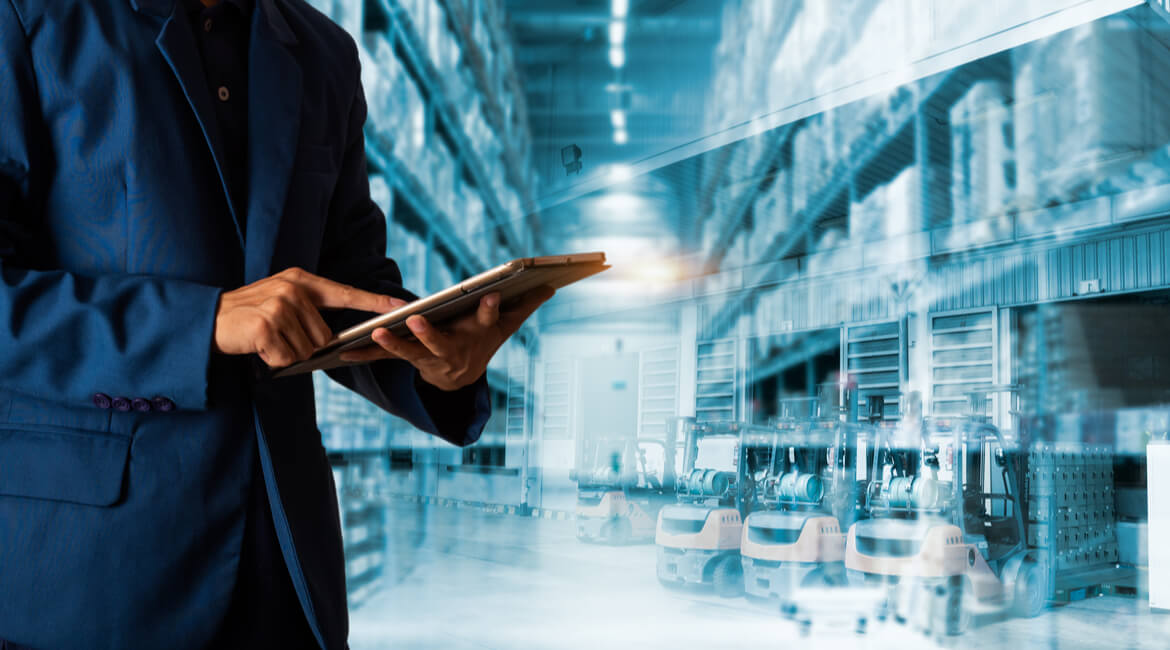
Internet of Things (IoT) and RTLS systems – combined with Artificial Intelligence (AI) as well – have enormous potential for logistics management: in fact, interconnection and creation of smart objects enable more streamlined and dynamic operating models.
In particular, a warehouse assets’ real-time management powered by RTLS technologies (Real-time Locating System) significantly improves processes: the use of resources, in such a regulated system, operates better and pays off.
The applications of IoT and RTLS to logistics management allow, therefore, to maximize the use of resources, such as material handling equipment (forklifts) and workers themselves. High levels of service, less time and costs, increased productivity and extreme adaptability to the context are just some of the benefits that can be obtained both by connecting assets to each other and by connecting assets and industrial systems (such as MES and WMS) – and, therefore, by data collection.
In a warehouse able to exploit the potential of IoT and Artificial Intelligence, uptime is, basically, more efficient: the work of operators is simplified, employees become more productive and, most of all, they’re safer. Not to mention all benefits that can be achieved in levels and quality of service, that reach extremely high standards.
Reducing inefficiencies in logistics management
The interconnection of assets and industrial systems intervenes on two key elements of logistics management: handling costs and accuracy of execution.
“Analog” systems have, in this perspective, an almost natural rate of criticality resulting from a less systematic and more limited approach. Reduced visibility in logistics processes leads here, in different ways, to delays, defaults and errors.
This means, for example, that locating and picking up loads’ operations become longer and harder to manage. And, as it should be remembered, picking, according to some statistics, impacts up to approximately 55% warehouse operating costs.
Furthermore, handling activities can be slowed down by a not very rational use of vehicles. This leads to queues, bottlenecks or assignment errors in the execution of missions.
Taken individually, these inefficiencies do not seem too serious. In general management, on the other hand, they have a significant weight that also turns into excessive costs and redundancies. More advanced models of logistics management have the potential to reduce up to 30% these costs .
The reduction of costs is achieved, after all, also by making the uptime of vehicles more rational and optimizing the number depending on the real demand.
Reducing costs whilst increasing productivity
A review of warehouse processes from an IoT perspective thanks to the support of Artificial Intelligence, can solve critical issues and optimize operations, whilst increasing productivity.
Take the case of RTLS systems, that is real time locating. These systems create high-visibility settings where assets get identified with extreme precision and speed, by exploiting the placement of devices for direct localization of material handling equipment, and indirect localization of the goods meant to be handled.
In terms of logistics management, this allows to achieve a significant reduction in handling times and an increase in service quality as well.
In particular, picking times and costs are reduced thanks to the introduction of IoT systems based on Artificial Intelligence. This, in fact, determines the best and always updated collection and delivery sequences, making uptime fluid, rational and super efficient.
By processing the information obtained locating vehicles combined with the list of missions in real time, AI algorithms can continuously adapt the execution to the context, controlling the assignment on a position basis and anticipating any critical issues. This way, misalignments, queues, and other potentially problematic events are solved in a timely manner, with an important return on the general uptime.
According to some statistics, in such a model of logistics management it’s possible to reduce error margins up to 67%. Once again, there’s a gain in efficiency thanks to the optimization of the resources used in warehouse operations.
Optimizing the use of resources
Enhanced logistics management with advanced solutions based on the combination of Artificial Intelligence and RTLS produces leaner operating models, that offer important advantages, including:
- productivity growth;
- a reduction of times, routes and related handling costs;
- a better use of resources.
Simply put, logistics processes become more productive and cost-effective. And this allows, in fact, to create a more rational use of resources. This happens because, for instance, routes meant to be covered and workloads become more precisely defined, allowing to reduce unladen journeys for forklifts and potentially reducing the number of trucks needed for handling operations as well.
Again, data obtained from assets can be used to monitor the efficiency status of individual vehicles. This allows to prevent potential downtime related to maintenance, to manage malfunctions in a timely manner and, also, to extend the life cycle of a vehicle.
A logistics management governed by IoT-type solutions with RTLS and Artificial Intelligence, therefore, allows to operate with a more efficient use of resources. This way, the digitalization of processes, interconnection among assets and industrial systems, and localization in real time produce a significant efficiency in warehouse material handling.